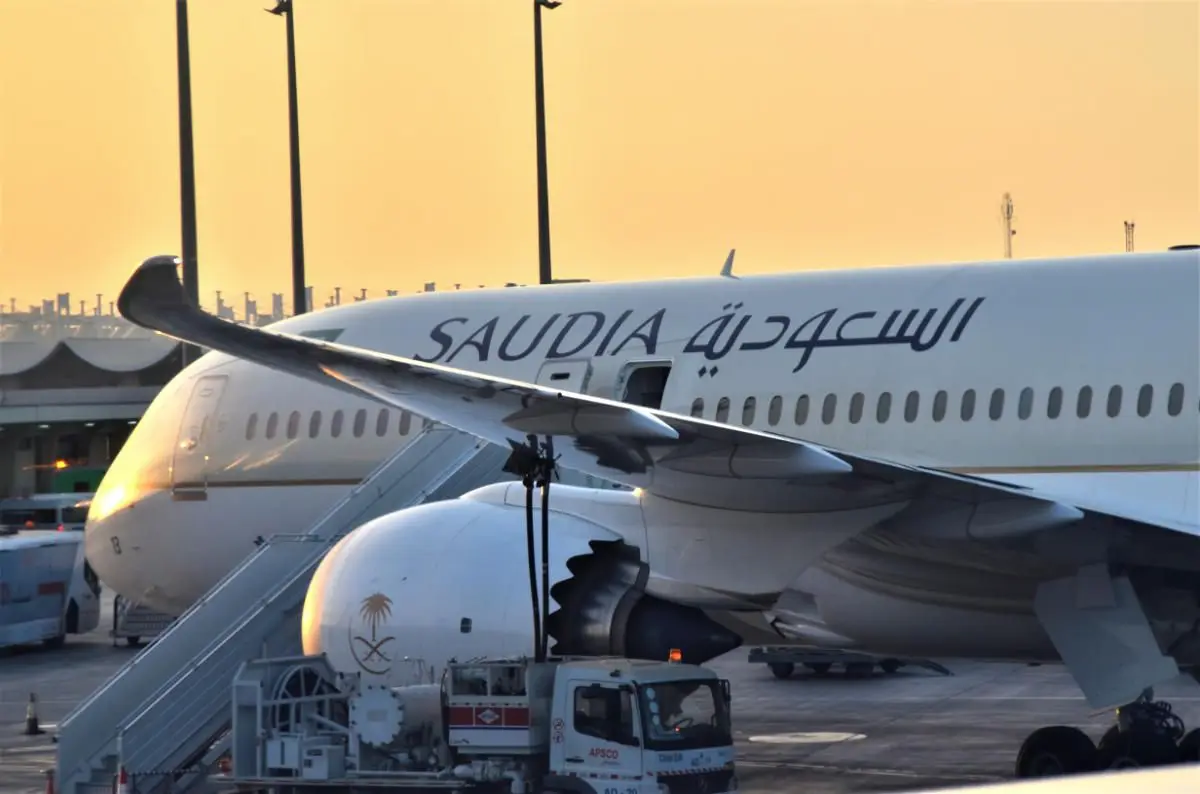
How Jet Fuel Is Made
Jet fuel is the lifeblood of modern jet aircraft. But how is jet fuel made?
Table of Contents
A jet engine requires fuel to propel the aircraft. But jet-powered aircraft cannot run on just any type of fuel.
Modern jet aircraft require fuel with a high energy content and good combustion properties. In addition, authorities and airlines require the fuel to be safe.
To produce jet fuel, oil producers need to drill deep into underground deposits for crude oil, and they need advanced manufacturing equipment for refining it.
In this post, we explore how jet fuel is made.
What Is Jet Fuel
Fuel for jet aircraft consists mainly of kerosene, a liquid, flammable hydrocarbon derived from crude oil. An advantage of jet fuel is that it burns relatively clean, with little to no residue, which makes kerosene ideal for aviation. Burning jet fuel only leaves water and carbon dioxide.
In addition to kerosene, fuel producers add several different additives to preserve the aircraft's engines and fuel systems, ultimately extending the airplane's life. Other additives increase flight safety.
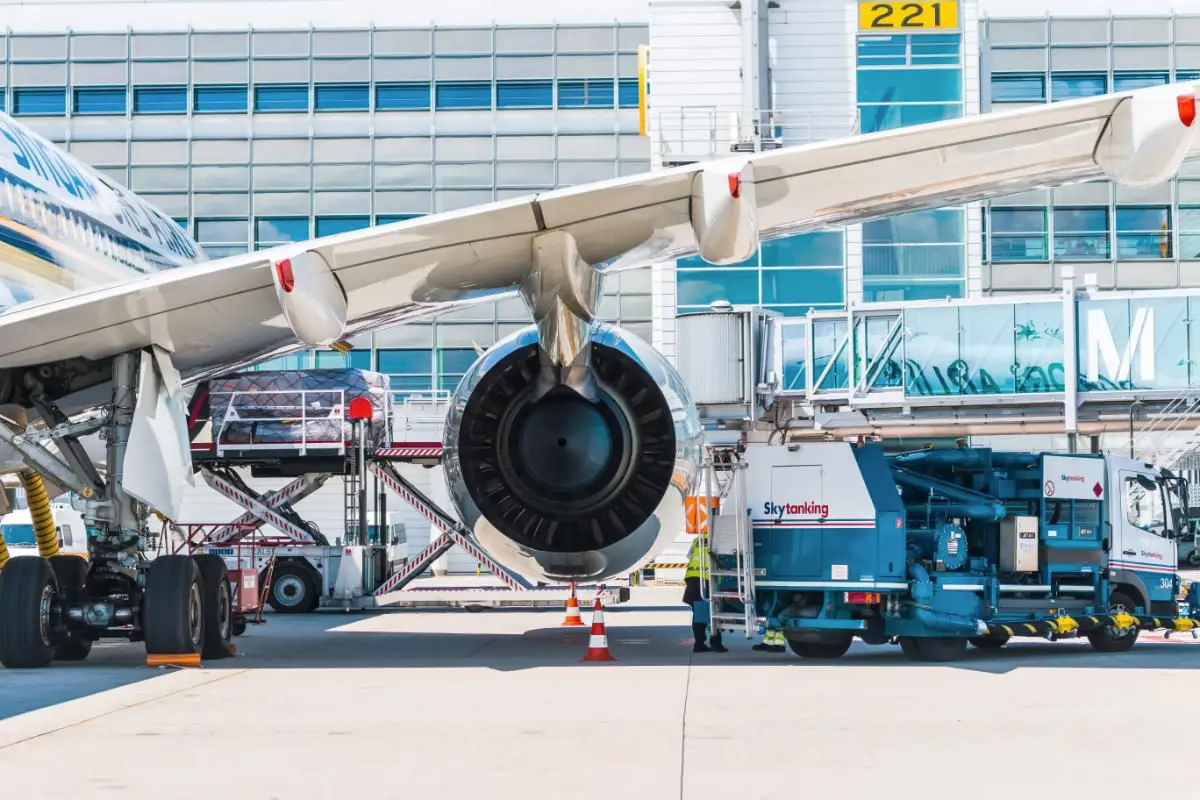
The most common types of civilian jet fuel are Jet A and Jet A-1. Another more specialized fuel for flying in freezing climates is also available called Jet B.
Crude oil varies in its composition, and that reflects on the jet fuel produced from it. Therefore jet fuel is defined by its performance characteristics instead of a pre-defined chemical compound.
How Jet Fuel Is Made
It all starts with crude oil or fossil oil. Crude oil mainly consists of hydrocarbons. In chemistry, a hydrocarbon is a molecule composed only of hydrogen and carbon.
Nature produces crude oil when large quantities of dead organisms like plankton and algae are buried underground and subjected to intense pressure and high temperatures.
Jet fuel production generally boils down to three overall steps. First, jet fuel producers need to extract the crude oil from the underground deposits. Next, a refining process separates the crude oil into various components such as gasoline, diesel, and kerosene. The last step is adding additives to the jet fuel.
Extraction
Several technical differences exist for extracting the crude oil from the underground depending on where the oil is and the overall geological conditions. However, the general process is similar.
Oil producers extract crude oil from underground deposits using drilling techniques. Depending on where the oil is, the drilled holes can be several thousand meters deep. Drilling technicians can even drill sideways to overcome obstacles better and reach crude oil reservoirs farther away.
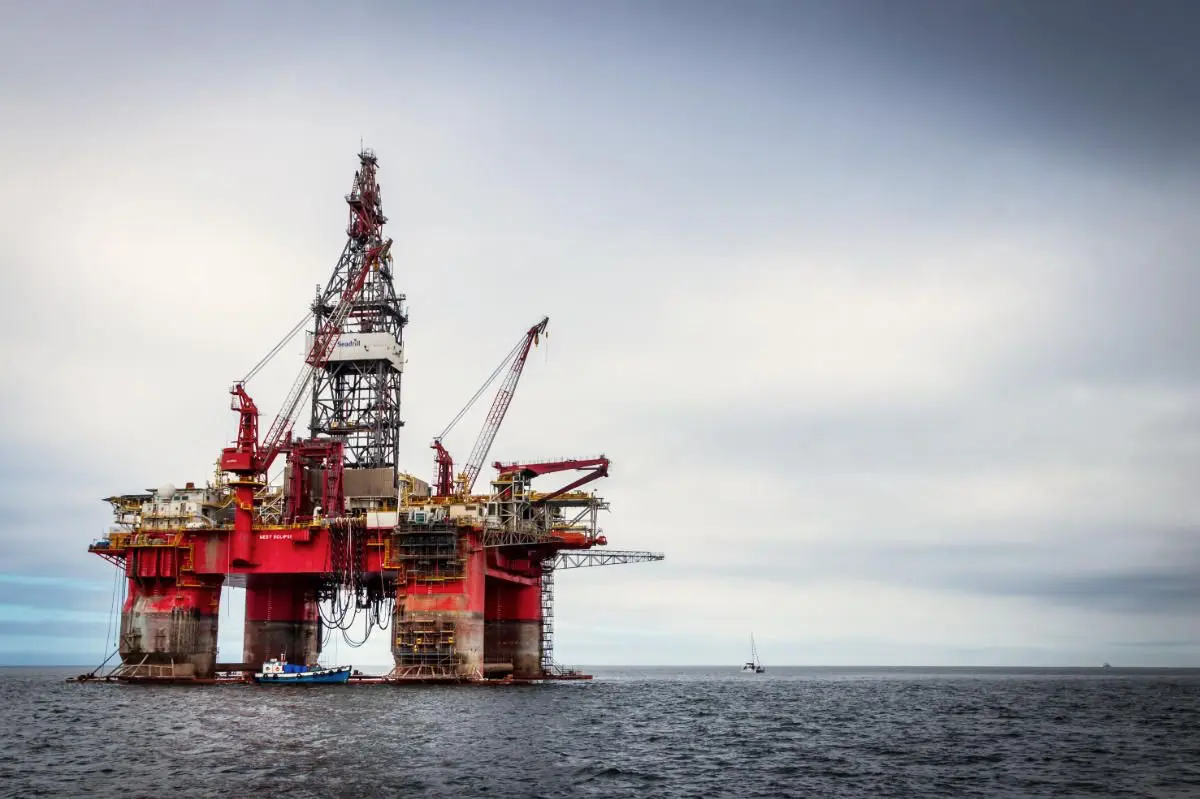
As crude oil is liquid, it can flow through a pipeline, which the technicians install in the drilled hole. A phenomenal amount of technology goes into the entire drilling process, especially when drilling offshore. Here, the environment makes it more complex, and extracting crude oil requires more steps, requiring more advanced equipment.
Through the pipeline and borehole, oil producers pump up the crude oil. Then they transport it via land or sea to a refining facility.
Refining
The refining starts with a process called distilling.
A furnace superheats the crude oil to 400°F, and the oil turns into gas. After that, large pipes lead the gas into the bottom of a distillation tower.
In the distillation tower, the crude oil gas rises upwards and cools down underway. The temperature decreases towards the top. When the gas cools down, it condenses and turns back into liquid form.
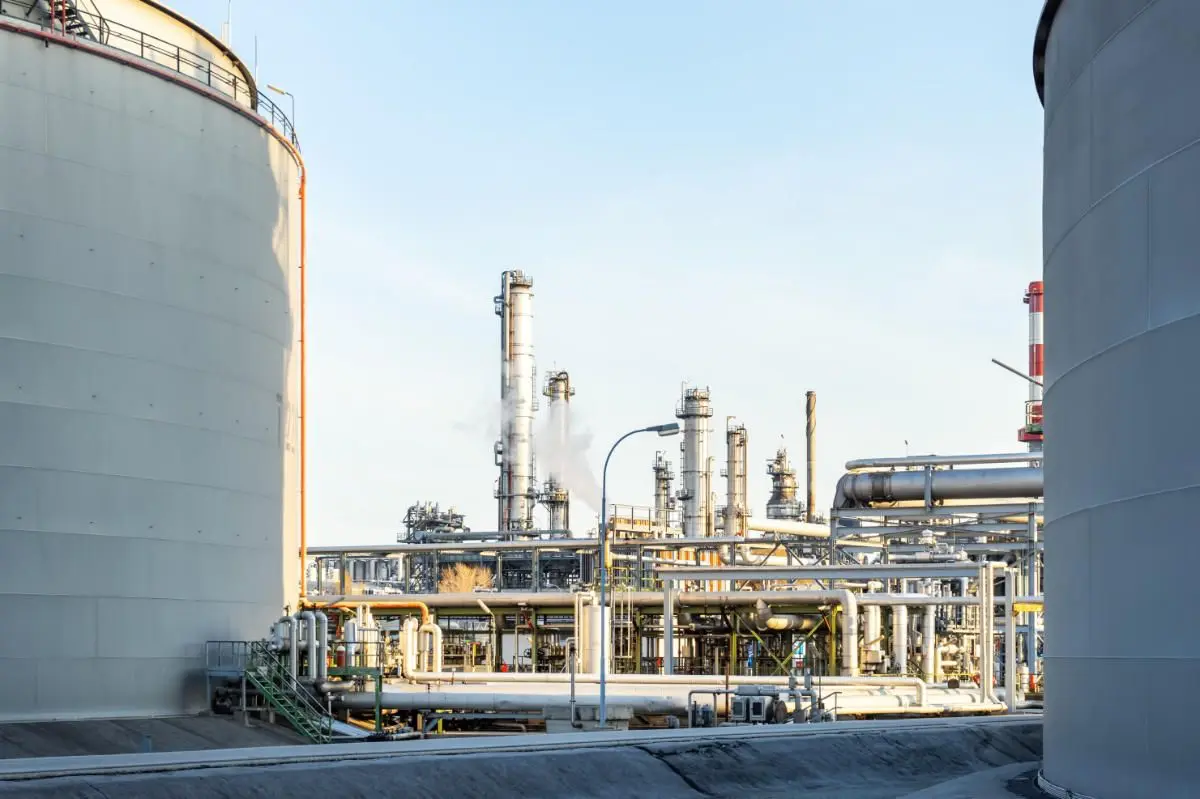
As mentioned, crude oil consists of many different hydrocarbons, and these have varying boiling points. That means that, if in gas form, they turn back into liquid at different temperatures. So as the superheated crude oil vapor rises towards the top of the distillation tower, the components cool down at various heights.
For example, gasoline (or petrol) turns back into liquid at 85°F (30°C) near the top of the tower. The hydrocarbons that make up diesel condenses at 500°F (260°C) closer to the bottom of the tower.
Kerosene for jet fuel turns back into liquid form at around 350°F (180°C).
Different floors inside the distillation tower collect the now-liquid products at their respective temperature stages. Now, pumps tap off the products, and another separate process removes the sulfur from them.
The next step is preparing the kerosene for use on jet aircraft by adding additives.
Additives
Fuel producers add several different additives to the kerosene, and each of them has a specific purpose.
One of the additives is a corrosion inhibitor that prevents corrosion in the aircraft's fuel tanks, fuel lines, and engines. This additive helps preserve the aircraft and extend its life.
Jet fuel always contains a small amount of water, as complete removal of it is impossible. But even in these small amounts, the water can freeze into crystals and potentially clog the airplane's fuel system, posing a potential safety risk. To counter this, jet fuel producers add an icing inhibitor that prevents ice crystals from forming in the fuel at low temperatures.
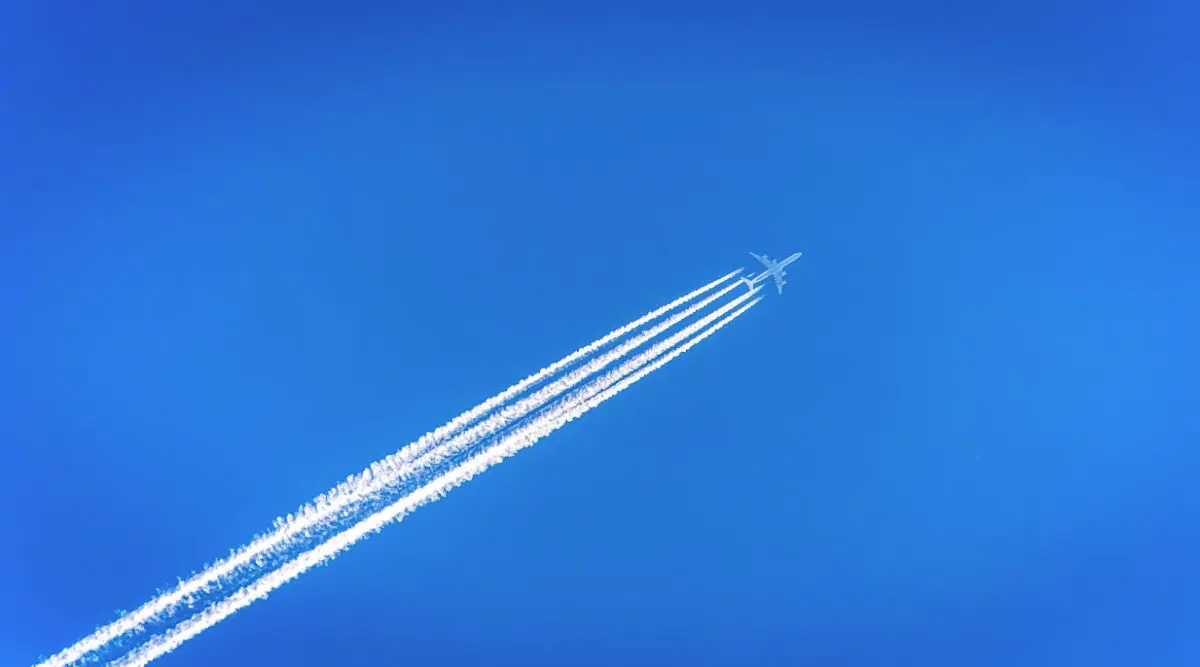
Other additives can include a metal deactivator additive that reduces the effect of any dissolved metals in the jet fuel as this can affect engine stability.
Finally, an anti-static additive can minimize the buildup of static electricity generated by fuel movement.
Conclusion
Jet fuel consists mainly of kerosene with a small amount of additives added.
Kerosene is a flammable, liquid hydrocarbon that comes from crude oil. The additives give the fuel some desirable properties, help preserve the aircraft, and increase flight safety.
If you want to read more about the types of airplane fuel and some more sustainable alternatives, check out this post.
Planenerd Newsletter
Join the newsletter to receive the latest updates in your inbox.