How Are Jet Engines Tested? Inside the Rigorous Testing Process
Jet engines undergo rigorous testing before being used in aircraft. Learn about the various testing procedures and quality control measures involved in ensuring the safety and efficiency of jet engines.
Table of Contents
Jet engines are among the most sophisticated pieces of engineering ever created. They power the world’s airliners, enabling millions of flights each year with incredible efficiency and reliability. But have you ever wondered how manufacturers ensure these engines can withstand the extreme conditions of flight before they’re installed on an aircraft?
Every jet engine undergoes a rigorous series of tests designed to simulate real-world flying conditions—and far beyond. From pushing engines to their absolute limits in test facilities to firing birds and ice into running turbines, each test is critical for ensuring safety, performance, and durability.
In this post, we’ll take a deep dive into the extensive testing process that jet engines must go through before they’re cleared for commercial use.
Why Jet Engine Testing is Critical
Jet engines operate in some of the most extreme conditions imaginable. At cruising altitude, these engines must function reliably while enduring temperatures as low as -60°C (-76°F) outside, while their internal core can exceed 1,500°C (2,732°F). They are responsible for generating immense amounts of thrust, often exceeding tens of thousands of pounds, all while maintaining fuel efficiency and stability over thousands of flight hours.
Given these demanding conditions, jet engine failures cannot be left to chance. Rigorous testing is essential to ensure engines can handle everything from severe weather to sudden thrust changes and even unexpected encounters with airborne debris.
The Stakes of Jet Engine Reliability
The potential consequences of an engine failure are serious, especially at high altitudes. While modern aircraft are designed to fly safely even if one engine malfunctions, reliability is paramount in commercial aviation. Engine manufacturers must prove that their designs can:
- Operate continuously for thousands of hours without significant wear or performance degradation.
- Withstand extreme conditions such as heavy turbulence, icing, and high-altitude air pressures.
- Handle rare but critical scenarios like bird strikes or volcanic ash encounters.
Failures in engine design or insufficient testing can lead to dangerous situations in flight, costly repairs, and even regulatory grounding of entire aircraft fleets. Some of history’s most famous aviation incidents have led to stricter testing protocols aimed at preventing such failures in the future.
Continuous Advancements in Testing
Jet engine testing has evolved significantly over the decades, incorporating advanced technologies such as high-speed sensors, artificial intelligence, and digital simulations. Today, testing is not just about survival—it’s also about efficiency. Airlines demand engines that burn less fuel, create lower emissions, and operate with minimal maintenance requirements.
The goal of jet engine testing is simple: ensure that every engine installed on an aircraft is reliable, durable, and able to perform safely under virtually any condition.
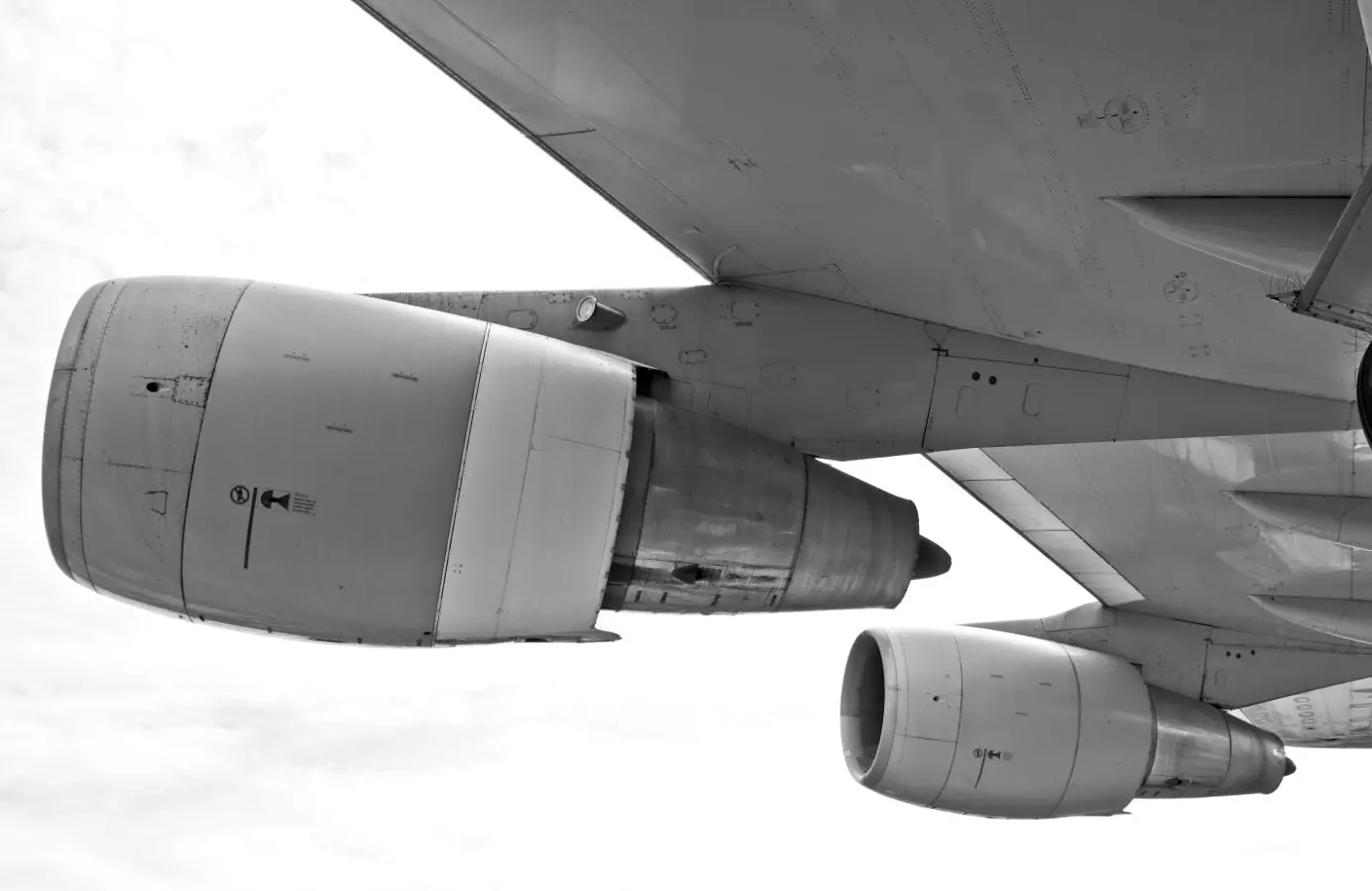
Types of Jet Engine Testing
Before a jet engine is ever installed on an aircraft, it must pass a series of rigorous tests designed to evaluate its performance, durability, and safety. These tests are conducted at various stages of development, from early prototypes to fully assembled engines ready for commercial use.
Below, we’ll explore the key types of jet engine testing and how manufacturers ensure these powerful machines can handle real-world flight conditions.
Design and Development Testing
Before an engine even enters physical production, extensive design testing takes place using cutting-edge computer simulations and wind tunnel experiments. Engineers utilize Computational Fluid Dynamics (CFD) software to model airflow, combustion efficiency, and thermal behavior.
Once a prototype is built, components like turbine blades and combustors are tested individually in laboratory settings. These early tests help refine engine architecture before moving on to full-scale testing.

From early prototypes to fully constructed engines that are prepared for commercial use, jet engines are tested at several phases of development. Photo by Rolls-Royce plc / Flickr.
Factory Testing (Before Installation on Aircraft)
Once an engine is assembled, it undergoes extensive ground testing in a specialized facility known as a test cell. This highly controlled environment allows engineers to run the engine at various power settings while measuring key parameters, such as:
- Thrust output and fuel efficiency
- Exhaust gas temperature
- Vibration levels and structural stability
- Oil and lubrication system performance
Modern test cells are equipped with high-speed cameras, laser sensors, and monitoring systems that assess the engine’s real-time performance. Any anomalies or inefficiencies detected during these tests must be addressed before the engine is cleared for the next stage.
Endurance and Stress Testing
Jet engines are designed to operate reliably for tens of thousands of flight hours, often with minimal maintenance. To evaluate long-term performance, endurance tests simulate years of use within a compressed time frame.
Engines are run continuously for hundreds of hours at varying power settings—including full throttle—to test wear and fatigue. Some tests even push engines well beyond normal operational limits, exposing them to extreme temperatures, high altitudes, and rapid power transitions to ensure they can withstand real-world stress.
Bird, Ice, and Debris Ingestion Tests
Aviation authorities require jet engines to be capable of surviving the ingestion of foreign objects during flight. To simulate these real-world hazards, manufacturers perform ingestion tests, where various materials are introduced into a running engine. Two of the most critical tests include:
- Bird Strike Testing: Using a specialized cannon, dead birds (typically chickens or gelatin-substituted materials) are fired into a spinning engine to simulate bird strikes and assess how the engine absorbs damage.
- Ice Ingestion Testing: Large chunks of ice are introduced into the engine to evaluate how ice buildup affects performance. Jet engines are equipped with anti-icing systems to prevent ice accumulation, and these tests ensure they function as expected.
In addition, tests may introduce volcanic ash, hail, and small debris to evaluate how engines respond to environmental hazards.
Water and Hail Resistance Testing
Engines frequently operate in heavy rain and extreme thunderstorms, making water ingestion tests a critical part of engine certification. For these tests, high-speed water sprays are directed into running engines to simulate flight through torrential downpours. Engineers assess drainage, combustion stability, and power response to ensure safe operation in wet conditions.
Some facilities also simulate severe hailstorms to determine if the fan blades can handle impacts without sustaining damage that could compromise engine integrity.
Blade Containment and Failure Testing
One of the most dangerous potential engine failures is a blade-out event, where a fan or turbine blade detaches at high speeds. If an engine isn’t designed to contain such failures, debris could puncture the fuselage or fuel tanks, leading to catastrophic consequences.
To assess containment capabilities, manufacturers perform blade-off tests, where they intentionally detach a turbine or fan blade during operation. The engine’s protective casing must effectively contain the broken component, ensuring that debris does not escape. This rigorous test helps improve safety designs and prevent disaster in the unlikely event of an actual engine failure.
Flight Testing on Aircraft and Testbeds
Before an engine receives final certification, it must undergo flight testing. In many cases, manufacturers install the new engine onto a modified test aircraft—typically an older Boeing or Airbus model—where it is evaluated in real-world flying conditions.
During flight testing, engineers assess how the engine performs under:
- Various altitudes and airspeeds
- High-thrust and low-thrust conditions
- Sudden throttle adjustments (rapid acceleration and deceleration)
Certification and Regulatory Approvals
Even after passing an extensive series of performance and endurance tests, a jet engine cannot be installed on a commercial aircraft until it is officially certified by aviation regulatory authorities. Organizations such as the Federal Aviation Administration (FAA) in the United States and the European Union Aviation Safety Agency (EASA) in Europe have strict requirements that every aircraft engine must meet to be deemed airworthy.
The Engine Certification Process
The certification process for a new jet engine can take several years and involves a combination of laboratory testing, real-world flight validation, and regulatory review. The key steps include:
- Preliminary Design Approval – Before physical testing begins, the manufacturer submits detailed engine design documentation to the certifying authority, ensuring it aligns with airworthiness standards.
- Ground Testing Verification – Regulators oversee extensive ground testing, verifying that the engine successfully meets structural and performance requirements.
- Flight Testing Evaluation – Engines are installed on test aircraft and flown under various real-world conditions while regulatory inspectors monitor their reliability and efficiency.
- Extended Operation Trials – Some engines undergo ETOPS (Extended-range Twin-engine Operational Performance Standards) certification, which is essential for twin-engine airliners operating long-haul routes over oceans and remote areas. The tests validate that an aircraft can continue flying safely for a specified duration (often 180 minutes or more) on just one engine in case of failure.
- Emissions and Noise Compliance – Modern jet engines must comply with strict environmental regulations set by the International Civil Aviation Organization (ICAO), ensuring reduced emissions and lower noise pollution.
- Final Regulatory Approval – Once all tests are successfully completed, regulators issue a Type Certificate, officially clearing the engine for use in commercial aircraft operations.
Ongoing Monitoring and Post-Certification Testing
Certification is not the end of regulatory oversight—far from it. Even after an engine enters active service, manufacturers and airlines must continue monitoring performance to ensure long-term safety and reliability.
- In-Service Performance Data – Airlines and engine manufacturers track real-time data from operational aircraft to detect potential issues before they lead to failures. Advances in predictive maintenance—using AI and big data analytics—help airlines address wear and tear proactively.
- Recurring Safety Inspections – Aviation authorities periodically conduct audits and inspections to ensure compliance with evolving safety regulations.
- Response to Real-World Incidents – If an engine experiences an issue in airline operations—such as abnormal wear, uncontained failures, or design flaws—regulators may issue Airworthiness Directives (ADs) to mandate modifications, inspections, or additional testing.
How Jet Engine Testing Improves Passenger Safety
While jet engine testing may seem like an engineering challenge confined to laboratories and manufacturing plants, its real-world impact is felt by every airline passenger. The extensive testing and certification process ensures that every commercial flight operates with an engine capable of handling almost any condition, making air travel one of the safest modes of transportation.
Reducing the Risk of In-Flight Engine Failures
The most obvious benefit of rigorous engine testing is reliability. Every commercial airline engine is designed to operate for thousands of flight hours without failure, and real-world engine failures are exceedingly rare. Even in the rare case that an engine malfunctions, modern commercial aircraft can safely continue flying and land with the remaining engine(s).
Jurisdictions like the FAA and EASA require ETOPS (Extended Twin-Engine Operations) certification, ensuring that twin-engine aircraft can continue flying safely for an extended period—even with one engine disabled. This is why twin-engine aircraft like the Boeing 787 and Airbus A350 can fly long-haul routes over oceans with confidence.
Enhanced Safety from Environmental Hazard Testing
Many travelers are unaware of the external threats that a jet engine must be able to withstand. Thanks to years of rigorous testing, modern jet engines are built to handle:
- Heavy rain and thunderstorms—Ensured by water ingestion tests.
- Icing conditions—Validated through simulated ice buildup and ingestion tests.
- Bird strikes—Mitigated through blade containment and impact resistance testing.
By designing engines to handle these potential hazards, the aviation industry significantly reduces the risk of incidents caused by environmental factors.
Making Jet Engines More Efficient and Reliable
Engine testing isn't just about safety—it also helps improve performance and fuel efficiency. Airlines rely on engines that can provide:
- Lower fuel consumption, reducing operating costs and carbon emissions.
- Quieter operation, making flights more comfortable for passengers and reducing noise pollution near airports.
- Longer maintenance intervals, ensuring fewer disruptions to airline schedules and better reliability for travelers.
As testing methods and engine designs improve, modern engines become lighter, more powerful, and more efficient—ultimately benefiting both airlines and passengers.
Lessons from Past Incidents: How Testing Continues to Improve
Many advances in jet engine testing and certification have come from real-world aviation incidents. For example:
- United Airlines Flight 232 (1989)—A catastrophic engine failure led to improvements in blade containment testing and materials used in turbine components.
- US Airways Flight 1549 (2009)—The "Miracle on the Hudson," where a bird strike caused dual engine failure, reinforced the importance of bird ingestion testing and emergency response training.
- Southwest Airlines Flight 1380 (2018)—A fan blade detached mid-flight, leading to enhanced inspection procedures for aging engine components.
Each incident serves as a lesson that fuels improvements in testing and maintenance, making future flights even safer.
What This Means for Passengers
For the average traveler, jet engine testing may be an invisible aspect of flying, but its impact is undeniable. Every time you step onto an airplane, you’re boarding an aircraft powered by engines that have been subjected to some of the most extreme testing conditions imaginable. This ensures that:
- Your flight is powered by one of the safest and most thoroughly tested machines in the world.
- Jet engines are designed to function reliably through rain, ice, turbulence, and other real-world conditions.
- Airlines operate with engines that are fuel-efficient, quiet, and built to last.
Conclusion
Jet engines are marvels of modern engineering, and their rigorous testing process ensures that they are among the most reliable machines ever built. From enduring bird strikes to withstanding extreme temperatures, every jet engine undergoes years of development and verification before carrying passengers.
The next time you board a plane, remember that the engine powering your journey has already been pushed to beyond its limits—many times over—to ensure your safety. Jet engine testing is a testament to the aviation industry's unwavering commitment to reliability, efficiency, and passenger security.
Also read:
Planenerd Newsletter
Join the newsletter to receive the latest updates in your inbox.