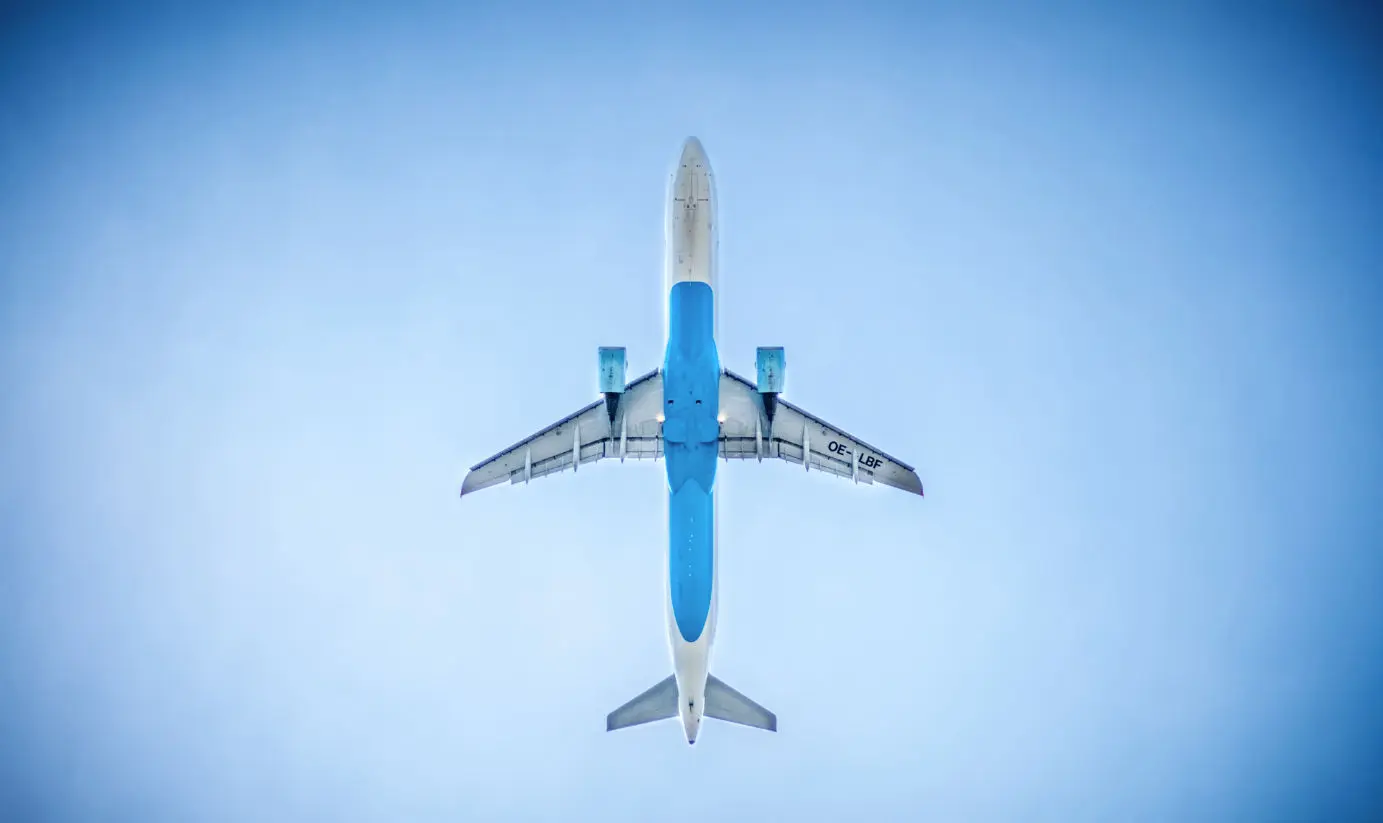
The Backbone of Flight: Understanding Aircraft Airframes
The airframe of an aircraft refers to the structure or frame that supports all other components, including the fuselage, wings, tail, and landing gear. Learn more about the importance and components of an aircraft airframe.
Table of Contents
In aviation, the airframe is the unyielding foundation upon which every aircraft is built. From small single-engine airplanes to massive commercial jumbo jets, understanding the intricacies of airframe design is helpful for aviation enthusiasts and professionals alike.
This article delves deep into airframes, examining their importance and shedding light on the key elements that make them the backbone of aircraft design. We also look at the materials used, the structural design considerations, and the impact on performance and safety.
What Is an Airframe?
The term "airframe" refers to the mechanical structure of an aircraft, excluding its powerplant. It encompasses the fuselage, wings, tail assembly, undercarriage, and supporting structures that hold the various components together. The airframe provides the necessary strength, rigidity, and aerodynamic shape for flight.
Airframes come in various shapes and sizes, depending on the aircraft type and intended purpose. Whether it's a glider, a fighter jet, or a commercial airliner, the airframe serves as the foundation for the entire aircraft.
Fuel efficiency is crucial when it comes to aircraft. Therefore, the components that make up the airframe are usually made of lightweight but strong materials like aluminum or composites.
Components of an Airframe
An airframe consists of several vital components that work together to ensure the structural integrity and functionality of the aircraft. These components include the fuselage, wings, empennage (tail assembly), and landing gear.
- Fuselage: The fuselage is the main body of the aircraft, housing the cockpit, passenger cabin, cargo compartments, and other essential systems. It provides the necessary space for occupants, cargo, and equipment.
- Wings: The wings generate lift, allowing the aircraft to stay airborne. They are attached to the fuselage and typically include additional structures like flaps and ailerons for control.
- Empennage: The empennage, located at the aircraft's rear, consists of the horizontal and vertical stabilizer. These structures provide stability and control during flight.
- Landing Gear: The landing gear supports the aircraft's weight during takeoff, landing, and ground operations. It typically includes wheels, struts, and shock absorbers to provide a smooth landing and takeoff experience.
Different Types of Airframes
Airframes can be classified into three types based on design, purpose, and construction. Every kind of airframe has advantages and disadvantages, and the choice depends on factors such as aircraft size, intended use, and manufacturing capabilities.
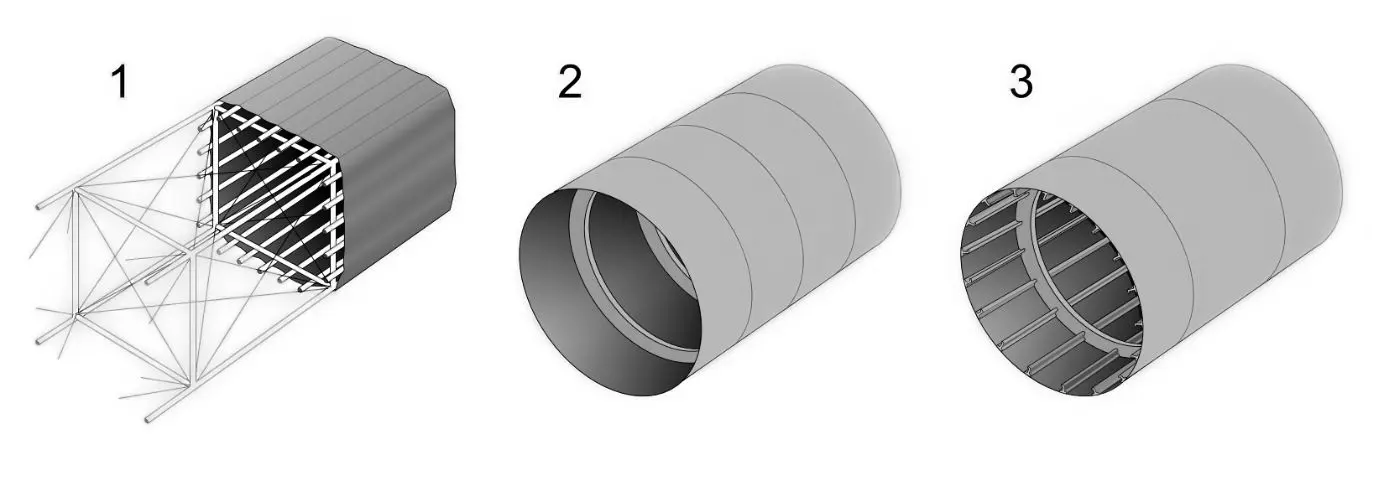
The three primary types of airframes are:
Conventional (or Truss)
The main characteristic of a conventional airframe is the use of a truss structure, which consists of interconnected beams arranged in a triangular pattern. These beams, often made of lightweight materials like steel or aluminum, are joined together with the help of bolts, rivets, or welded joints. The triangular shape of the truss provides strength and rigidity to the airframe. A conventional type airframe offers a simple and efficient design that has been widely utilized in the early development of aircraft.
One of the advantages of conventional airframes is their simplicity and ease of construction. The straightforward truss design allows for efficient manufacturing, maintenance, and repairs, thus reducing costs and time.
Monocoque
Monocoque airframes derive their structural strength from the external skin or covering. In a true monocoque, the external shell carries the loads, while frames and bulkheads shape the structure. The skin may be made up of lightweight materials like aluminum or composite materials. Monocoque airframes distribute the load evenly across the structure, providing strength, durability, and relatively low weight.
Monocoque structures offer a higher strength-to-weight ratio but require careful design considerations to distribute the loads evenly.
Semi-Monocoque
Semi-monocoque airframes combine elements of both conventional and monocoque designs. They combine a lightweight internal framework with a stressed skin. The internal framework called the fuselage framework, is made up of bulkheads, longerons, frames, and stringers. The stringers are thin, longitudinal beams that run the length of the aircraft, providing additional stiffness and support to the skin.
The skin of a semi-monocoque airframe is typically made of thin sheets of aluminum alloy, which are attached to the framework using rivets or adhesives. The skin is designed to carry some of the structural loads, but it primarily acts as a covering to maintain the shape and aerodynamic efficiency of the aircraft.
The combination of the internal framework and the skin in a semi-monocoque structure allows for a more efficient distribution of loads, improving overall strength and stiffness.
Semi-monocoque airframes are commonly used in modern aircraft due to their lightweight yet robust construction. They offer a good balance between strength, weight, and cost.
The Role of Airframes in Aircraft Performance
The airframe plays a crucial role in determining the overall performance of an aircraft. Several key factors are considered during the design process to optimize performance.
- Aerodynamics: The shape and outer contour of the airframe significantly impact the aircraft's aerodynamic efficiency. The airframe shape, including airfoils and winglets, helps to reduce drag, improving fuel efficiency and overall performance. Streamlined designs minimize drag and allow smoother airflow, improving fuel efficiency or higher speeds.
- Structural Integrity: The airframe must be designed to withstand the various forces imposed during flight, such as lift, turbulence, engine thrust, takeoffs, and landings. The airframe distributes the loads and handles the stresses imposed on the aircraft. Structural calculations and thorough analysis ensure the airframe can handle the loads without deformation or failure.
- Weight and Balance: The airframe contributes to the aircraft's overall weight, which considerably affects flight performance. Reducing weight improves the aircraft's maneuverability, fuel efficiency, and range, resulting in better performance. Therefore, engineers carefully strive to keep the airframe as light as possible while maintaining rigidity.
- Stability: The stability and control characteristics of the aircraft are influenced by the design of the airframe. This includes the arrangement and form of the wings and tail section. The aircraft's control surfaces are located on the wings and tail section, thereby dictating the aircraft's maneuverability. The airframe affects the agility and responsiveness of the aircraft through the appropriate design and balancing of various parts. In addition, weight distribution across the airframe affects the aircraft's stability, maneuverability, and balance in flight. Engineers consider the placement of heavy components, such as fuel tanks and cargo areas, for an optimal center of gravity.
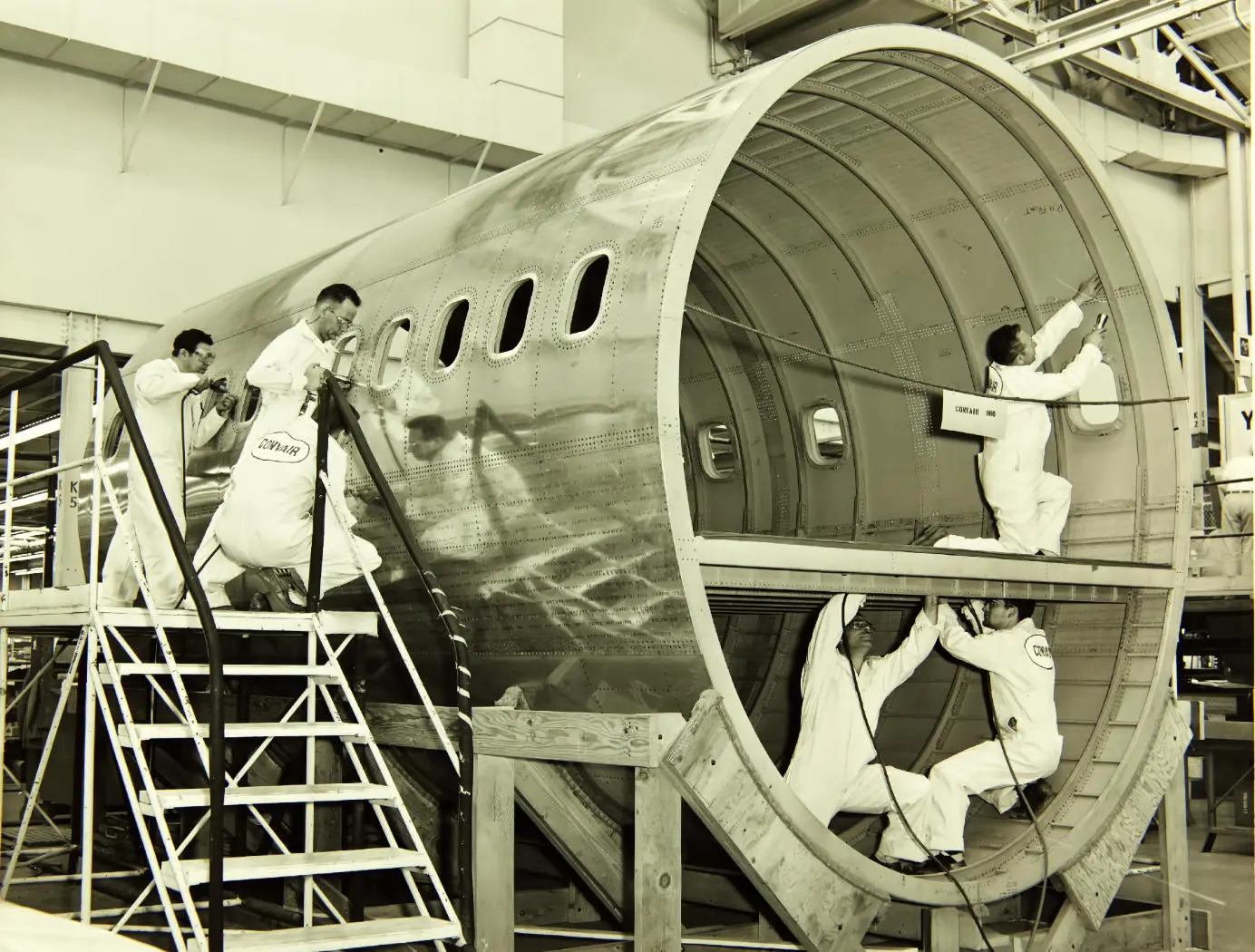
Factors to Consider in Airframe Design
Airframe design is a complex, lengthy, and expensive process that requires careful consideration of several factors. Some of the key considerations include:
Aerodynamics
A key aircraft consideration, aerodynamics, is a high priority when designing an airframe. The airframe should allow for low drag, efficient lift, and maneuverability.
Structural Integrity
During takeoff, flight, and landing, an aircraft undergoes varying stress levels on its structure. The airframe should be designed to handle these physical forces for decades of operation in all types of weather.
Weight
A lightweight airframe lowers fuel consumption while increasing payload capacity and range. Designers need to strike a balance between structural strength and weight.
Aircraft Purpose
The intended purpose of the aircraft influences the airframe design. Whether it's a long-range passenger aircraft, a cargo plane, or a military fighter jet, the airframe must be tailored to meet the specific mission requirements.
Manufacturability and Cost
The ease and cost of manufacturing and assembling the airframe components are critical considerations. Designing for manufacturability ensures efficient production and reduces costs.
Maintenance and Repair
Accessibility to critical components and ease of maintenance and repair are essential factors. Ideally, the airframe design should allow for efficient inspection, repair, and replacement of parts to minimize downtime and operational costs.
Environmental Impact
Airframe design also considers environmental concerns, such as noise reduction, fuel efficiency, and emissions. Advancements in materials and manufacturing techniques contribute to greener and more sustainable airframe designs.
Passenger Comfort
If the airframe is for a passenger aircraft, the design should consider passenger comfort, including cabin layout, noise reduction, and vibration control.
Airframe Materials and Construction Techniques
The choice of materials significantly impacts the airframe's performance, weight, and durability. Over the years, advancements in materials science have revolutionized airframe design.
Aluminum: Aluminum alloys have been widely used in airframe construction due to their lightweight properties, strength, corrosion resistance, and ease of manufacturing. However, aluminum has limitations in terms of stiffness and fatigue resistance.
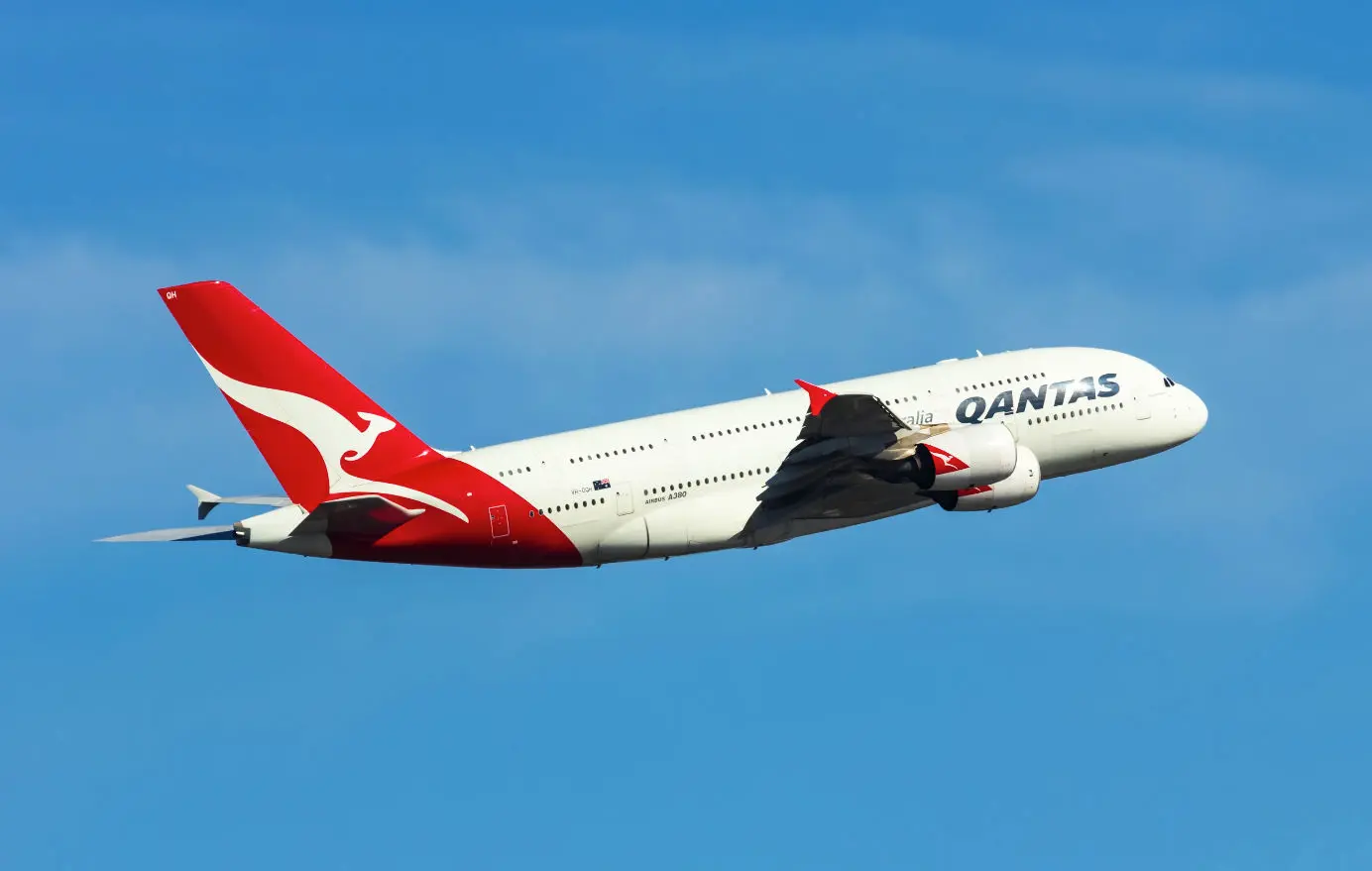
Titanium: Titanium and its alloys are known for their exceptional strength, lightness, and corrosion resistance. Titanium airframe components are commonly found in high-performance military aircraft and some commercial jets, where strength and durability are crucial. However, titanium is expensive and challenging to work with, requiring specialized manufacturing techniques.
Steel: Though less common in modern aircraft, steel is still used in some specialized applications, such as high-stress components. Steel airframe components offer excellent strength and toughness but are relatively heavy and prone to corrosion. Anti-corrosion measures like coatings or protective treatments are necessary.
Composite Materials: Composite materials, such as carbon fiber reinforced polymers (CFRP), offer significant weight savings and improved strength compared to traditional materials. Composites are highly corrosion-resistant and can be molded into complex shapes, allowing for more aerodynamically efficient airframes.
The choice of materials depends on cost, performance requirements, and manufacturing capabilities. Continued research and development in materials science will likely lead to even more innovative and lightweight airframe solutions.
Challenges in Airframe Design and Manufacturing
Airframe design and manufacturing pose several challenges that engineers must overcome to create safe and efficient aircraft.
- Structural Optimization
Designing an airframe that maximizes strength while minimizing weight is a delicate balance. Engineers must use advanced computer modeling and simulation tools to optimize the airframe's structural integrity and weight. - Certification and Regulations
Airframes (and aircraft in general) must meet stringent certification requirements and comply with aviation regulations to ensure safety. Designers must navigate complex rules and conduct extensive testing and analysis to obtain the necessary certifications. - Cost and Manufacturing Efficiency
Designing cost-effective airframes that can be efficiently manufactured is crucial for the aviation industry. Balancing performance, quality, and cost is a constant challenge in airframe design and production. Especially with many different materials and production techniques involved. - Innovation and Advancements
The aviation industry continuously evolves, and airframe design must keep pace with technological advancements. Manufacturers must stay up to date with the latest materials, manufacturing techniques, and design methodologies to push the boundaries of airframe performance.
Looking Forward - The Future in Airframe Design
As aviation technology advances and the world shifts to greener transportation, the future of airframe design must deliver a great deal.
Engineers and researchers are constantly trying to push the boundaries of what is possible, exploring innovative materials, manufacturing techniques, and design concepts.
Therefore, the future of airframe design is likely to focus on:
- Lighter and Sustainable Materials: Research in lightweight materials, such as carbon nanotubes and graphene, could lead to even more advanced and durable airframes. Sustainable and recyclable materials will also significantly reduce the environmental impact of airframe manufacturing and recycling.
- Advanced Manufacturing Techniques: Techniques like additive manufacturing, robots, and automation could improve airframe production in terms of production speed, precision, and costs.
- Adaptation to New Forms of Propulsion: The potential rise of electric and hybrid propulsion systems will likely influence airframe design to accommodate these technologies' unique requirements and constraints. Airframes must be optimized for efficiency, energy storage, and weight distribution.
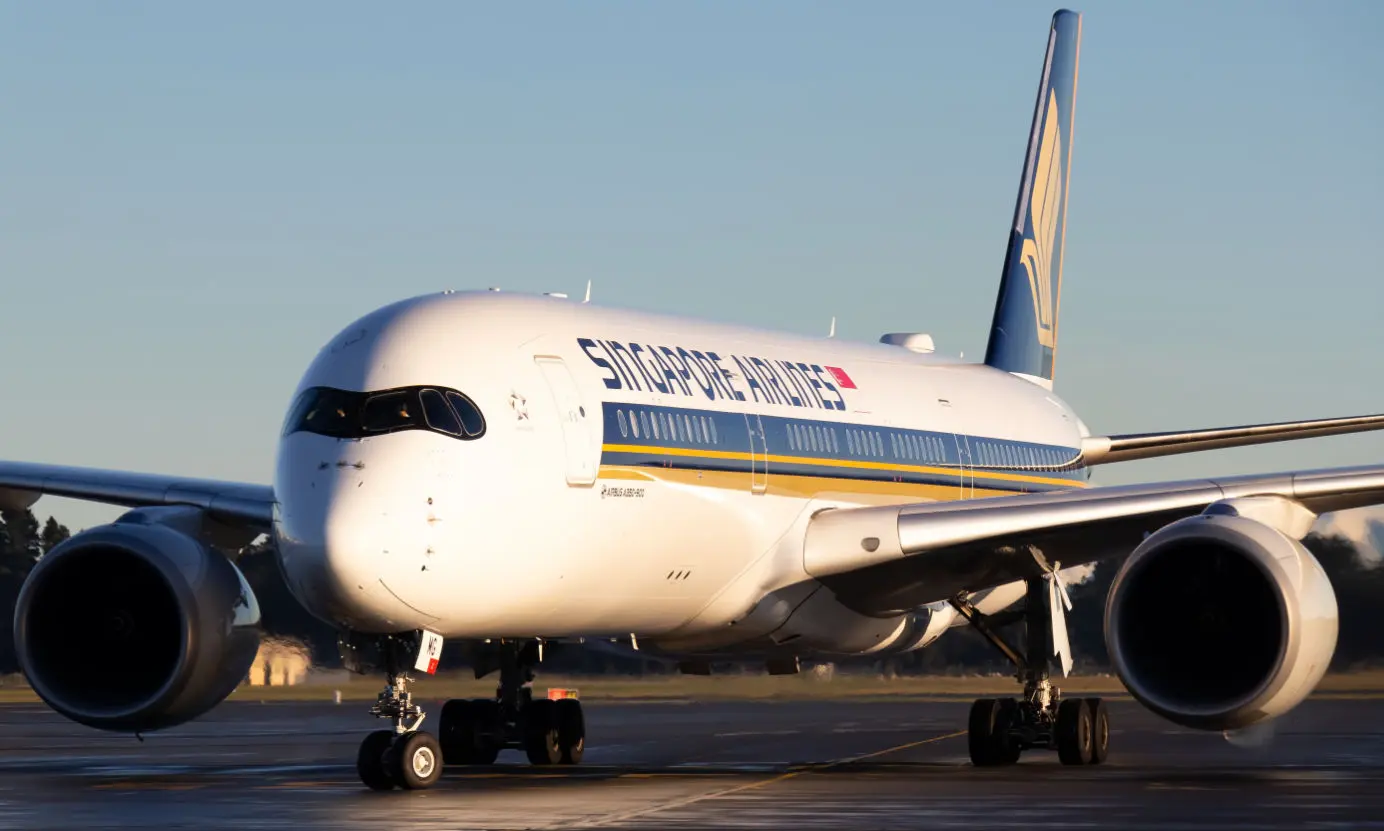
In summary, the future of airframe design will likely focus on lightweight materials, advanced manufacturing techniques, and new ways of propulsion. These advancements aim to make aircraft more efficient, environmentally friendly, and safer while improving the flying experience.
Conclusion
Airframes are the structural backbone of any aircraft, providing the necessary support and stability to ensure safe and efficient flight. From the fuselage to the wings, landing gear, and tail section, airframe components are crucial in maintaining aerodynamic integrity and distributing load forces during flight.
Throughout history, advancements in materials and design have revolutionized airframe construction, allowing for lighter and more fuel-efficient aircraft. From using aluminum alloys to adopting carbon composites, the aerospace industry continues to improve and innovate.
The development of airframes requires extensive research, engineering expertise, and rigorous testing to meet regulatory standards and industry demands. As technology continues to evolve, we can expect further advancements in airframe design, leading to more efficient and sustainable aviation in the future.
Airframes are not just the bones of an aircraft but a foundation of aviation. Whether carrying passengers, transporting goods, or conducting critical missions, airframes are at the heart of every flight.
Also read:
Planenerd Newsletter
Join the newsletter to receive the latest updates in your inbox.